News
Why 3D Parametric Architecture and 3D Printing Is About to Boom
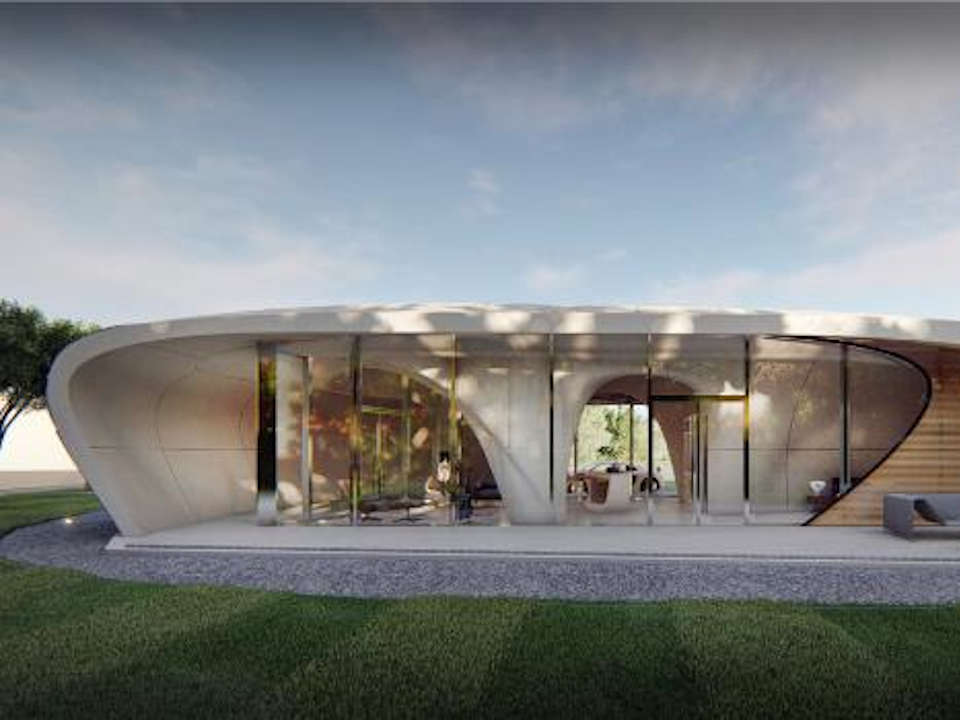
“Big box store.” It’s a pejorative term for a place where you shop for everyday items. You don’t go to the big-box store to find distinctive, quality products. A big-box purchase fills a need but isn’t likely to be the kind of thing you boast about to your friends. A big-box purchase is dull.
“Big box store.” It’s a pejorative term for a place where you shop for everyday items. You don’t go to the big-box store to find distinctive, quality products. A big-box purchase fills a need but isn’t likely to be the kind of thing you boast about to your friends. A big-box purchase is dull.
“Dull” also describes the big box building itself. And not just the big-box retail sites. Big-box everything. Office buildings. Schools. Government centers. Big box is tired. It’s common. It’s mundane. It’s boring.
Parametric Architecture
Parametric architecture, on the other hand, is the antithesis of big box. It is energetic. It is uncommon. It is imaginative. It is exciting. And it is sweeping the business of building design off its feet. Google “parametric architecture,” click on Images, and prepare to be stunned. These extraordinary structures have electrified architecture like nothing else in some time. The thing is, most exist only as designs, exquisite images languishing as 2D dreams on Google’s search results page.
Branch Technology seeks to change those 2D dreams into 3D realities. “We build next-generation exterior wall systems,” says Platt Boyd, founder and CEO of Branch Technology. “Our goal is the democratization of custom construction, making it accessible to a broad base of customers.” He cites a lack of innovation in design and construction as the source of the sameness we now endure. “We haven’t moved much beyond the post-and-beam construction that’s been around for ages.” Parametric architecture leaps far beyond post-and-beam.
3d printed houseLarge Scale 3D Printing
To create these innovative structures, Branch Technology uses another recent innovation: 3D printing, but on a construction scale. Their patented 3D printing process is called Cellular Fabrication and bears the trademarked term C-Fab. The massive printer produces a matrix of polymer in virtually any shape. The matrix is then filled with foam. A piece of the printed matrix the size of a concrete block weighs just two pounds supports 3,000 pounds in compression. Once filled with foam, its compression strength jumps to 6,000 pounds. Reliance on that matrix instead of a solid material means C-Fab uses 20 times less material than traditional 3D printing.
The process can be used to create complete structures where the 3D panels are the load-bearing components. But the greatest demand is from the commercial market where the pre-fabricated parts are attached to a building’s structure during construction and are not intended as load-bearing elements. It is an attached skin with an outer layer of glass fiber reinforced concrete (GFRC) for durability and protection from the elements. The pre-fab panel is four times stronger than a GFRC panel of the same shape and dimensions. Pricing is based on volume and Boyd says Branch Technology ships globally.
Because the manufacturing process is managed by computers, Branch Technology can use finite element analysis (FEA) to fine-tune aspects of the manufactured panels to meet local requirements. They have not, however, gone through the lengthy and costly process of getting their products rated in the many performance certifications that exist, such as seismic, hurricane and flooding.
The Technology Tipping Point
Parametric architecture is wildly popular in the architectural community right now. But are we at a tipping point where parametric architecture should be part of your business plan? Boyd says if we’re not there now, we soon will be. Here are the three reasons he thinks parametric architecture coupled with 3D printing is poised for explosive growth:
3D printing offers accessible design freedom. Boyd started as an architect, “and all those years I dreamed of having this freedom to create.”
Production is enabled by technology and a prefabrication process. Components are built with precision in a controlled environment unaffected by weather, hours of daylight or any of the other limitations present on a typical building site.
The end product is beautiful and identifiable. Commercial clients want their buildings to stand out and parametric architecture is the ideal means to make that happen.