Решения для ремонта и восстановления спецтехники
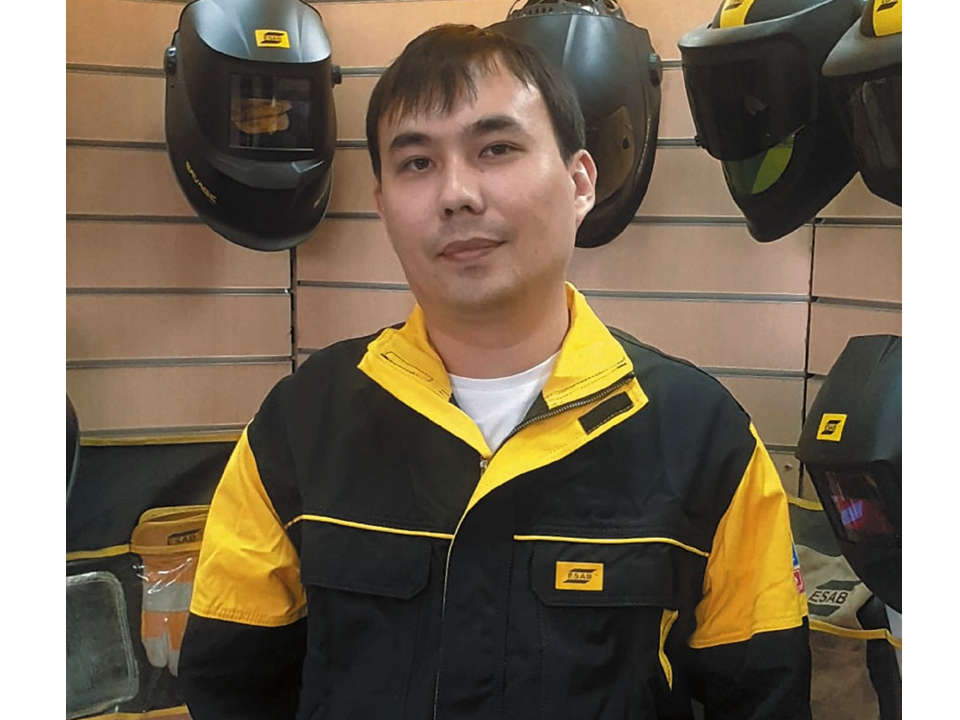
Давид Пак, руководитель направления Ремонт и Восстановление компании ESAB
Интенсивный износ деталей машин и механизмов происходит практически во всех отраслях промышленности, однако чаще остальных с ним сталкиваются в горнодобывающей, металлургической и строительной отраслях. Именно в этих индустриях оборудование ежедневно работает в условиях ударного воздействия, при повышенных температурах, а также при наличии абразива и коррозионной среды.
Износ бывает разным, к наиболее распространенным его видам относятся «контактная усталость» и «абразивный износ». Об основных причинах износа, его особенностях и современных решениях по его устранению рассказывает Давид Пак, руководитель направления Ремонт и Восстановление компании ESAB.
Давид, какое оборудование чаще всего сталкивается с износом?
– Запросы к нам поступают из самых разных отраслей промышленности, но в основном из тех, где рабочий процесс сопряжен с интенсивным износом оборудования. Чаще прочего от него страдают горно-шахтное оборудование и строительная техника, детали сельхозтехники, оборудование для цементной промышленности и металлургии.
В числе наиболее распространенного – детали и навесное оборудование для экскаваторов, погрузчиков, грейдеров, различные шнеки и буровые элементы, детали дробилок для переработки сырья. Большая часть обращений связана с потребностью в ремонте определенных деталей таких машин и механизмов, однако нередко мы сталкиваемся и с потребностью в превентивном увеличении их стойкости.
А какие основные причины изнашивания деталей?
– Износ деталей может наступить в результате развития усталостных явлений, имеющих термическую или контактную природу, а также наличия эрозионных процессов износа. При контактной усталости разрушение приповерхностных слоев металла наступает из-за трения, высокого давления, ударного воздействия, а также наличия абразива между парами трения. Такому виду износа подвержены, например, ж/д рельсы и крестовины. Горнодобывающему оборудованию в большей степени свойствен абразивный износ.
Наиболее эффективными способами увеличить прочность деталей являются наплавка и напыление, а также термическая химико-термическая обработка (ХТО).
Какие материалы и оборудование компания ESAB предлагает заказчикам для восстановительного ремонта и поверхностного упрочнения?
– Мы можем предложить оборудование и материалы практически для всех процессов. К наиболее распространенным материалам относятся электроды, сплошные и порошковые проволоки, ленты и флюсы. В исключительных случаях используются порошки для плазменной (PTA), лазерной наплавки, а также порошки или прутки для наплавки ацетилен-кислородным пламенем.
Наплавка может быть сделана газотермическим способом, с помощью дуговой сварки – электродами и проволокой в среде защитных газов, под слоем флюса или самозащитными проволоками. Также возможно применение менее распространенных процессов, таких как лазерная или плазменная наплавка.
Правда ли, что ключевым фактором в борьбе с износом является правильный подбор покрытия?
Универсальных материалов для этого не существует? – Да, это так. Для того чтобы определить наиболее стойкий материал в каждом конкретном случае, необходимо выявить преобладающий тип изнашивающего воздействия на поверхность. В то же время для борьбы с абразивным износом существует достаточно много процессов нанесения защитных покрытий на металлические поверхности: от практичной дуговой наплавки и различных видов напыления до лазерного плакирования.
В случае интенсивного абразивного износа на первый план выходят твердость наплавленного металла, наличие, размер и тип твердой фазы – карбидов. К наиболее износостойким покрытиям от этого вида износа относятся те, что содержат элементы вольфрама. Однако стоимость вольфрама растет, и многие предпочитают использовать более доступные материалы на железной основе с включениями карбидов хрома и боридов с твердостью наплавленного слоя 55–70 HRC.
Ведется ли разработка новых материалов для наплавки?
– Да, постоянно. Новые решения, которые мы разрабатываем в R&D центрах ESAB, основаны на потребностях рынка. Так, например, за последние два года, проанализировав запросы заказчиков в СНГ, мы разработали несколько видов наплавочных порошковых проволок. Сегодня эти продукты востребованы и за пределами содружества.
Важно понимать, что выбор конкретного процесса, оборудования или материала зависит от ремонтируемой детали и условий ее эксплуатации, требований и возможностей заказчика, а также условий ремонта. Это может быть как стандартное оборудование для ручной дуговой наплавки и сварки, так и оборудование, способное обеспечить механизацию, автоматизацию и роботизацию данных процессов. Мы подбираем для каждого заказчика индивидуальное решение.
Как вы определяете оптимальное решение для каждого конкретного заказчика, проводите расчеты?
– Прежде чем производить наплавку или ремонт, мы просчитываем их экономическую целесообразность. Для этого проводится анализ , который включает множество факторов – стоимость новой детали, ремонта, срок службы новой и отремонтированной детали , высчитывается , как долго прослужит наплавленный слой. Такие тесты мы проводим как на производственных площадях наших заказчиков, так и в нашем технологическом центре в Красногорске, когда габариты детали не слишком велики.
Бывает такое, что определенные детали машины или механизма сняты с производства или срок их поставки слишком велик, а простой оборудования чрезвычайно дорог.
В таких случаях нужно максимально продлить срок эксплуатации исходной детали, чтобы дотянуть до момента поставки замены.
Кроме того, простоев некоторого оборудования и вовсе допустить нельзя, поскольку это обойдется компании в миллионы рублей в сутки. Тогда надежность выходит на первый план, и применение поверхностной наплавки дает возможность ее обеспечить.