Анатолий Никитин: Развитие горного машиностроения в новых реалиях зависит от консолидированных усилий участников отрасли
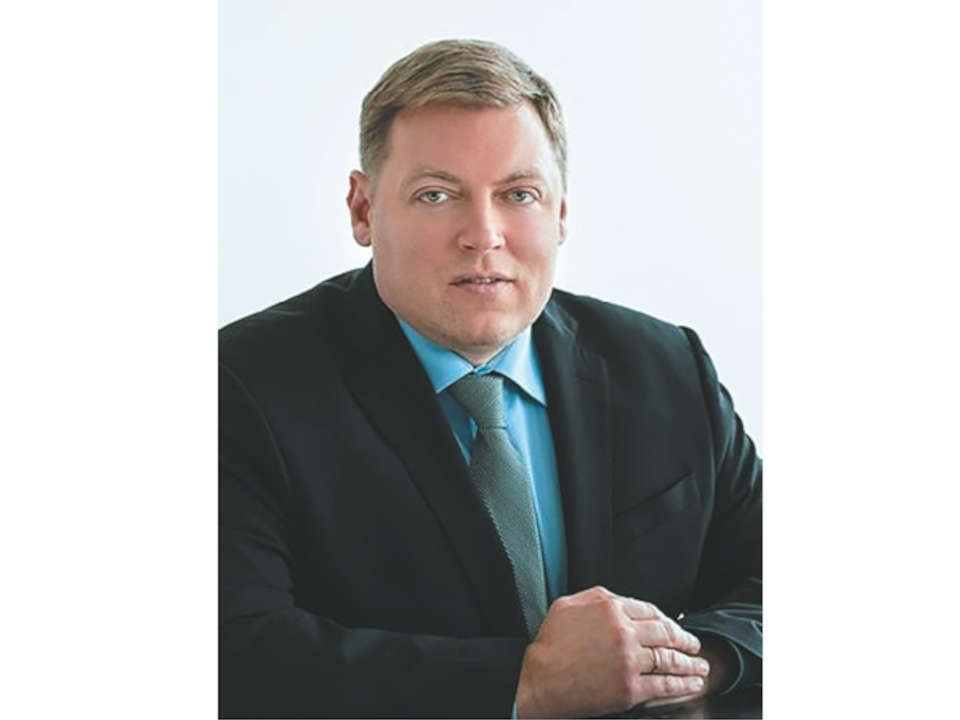
А.Ю. Никитин, Первый заместитель Председателя Высшего горного совета, Исполнительный директор НП «Горнопромышленники России»
2022 год становится новым вызовом для горного машиностроения. Сложность обстоятельств определяется санкционным давлением, ситуацией с кредитованием и другими аспектами. Железорудный и угледобывающий сектора экономики, в частности, нуждаются в реструктуризации кредитной нагрузки, доступном заемном финансировании и субсидировании ставок по кредитам. О том, что в отрасли также необходима единая информационная платформа сбора и удовлетворения потребностей в кадрах, оборудовании, финансировании, и о том, как выработать механизмы защиты внутреннего рынка от недобросовестной конкуренции, стимулировать объединение в инновационные промышленные кластеры, поговорили с Первым заместителем Председателя Высшего горного совета, Исполнительным директором НП «Горнопромышленники России» А.Ю. Никитиным.
В 2022 г. усилилось санкционное давление на экономику и финансы России. Проблема импортозамещения становится актуальной как никогда. Как сегодня можно оценить зависимость отраслей горной промышленности от импорта горно-шахтного оборудования?
– Конечно, такая зависимость есть. Согласно стратегии развития тяжелого машиностроения, разработанной Минпромторгом России, к 2030 г. объем российского рынка горного оборудования должен достичь порядка 170 млрд руб.
Пока же из года в год мы видели усиление зависимости российских шахт и разрезов от импорта оборудования, используемого в основных процессах производства. В 2011 г. количество импортного оборудования составляло 61,1%* от общего его объема на предприятиях отрасли (по шахтам – 45,9%, разрезам – 67,7%), в 2014 г. количество импортного оборудования составляло 72,5% от общего его объема на предприятиях отрасли (по шахтам – 52,4%, разрезам – 80,9%), в 2016 г. оно возросло до 75,5% (по шахтам – 54,5%, разрезам – 83,3%), в 2020–2021 гг. составило 76,6% (по шахтам – 53,1%, разрезам – 84,7%), хотя на значительную часть номенклатуры горно-шахтного оборудования есть российские аналоги.
При этом практически десятилетие, с 2011 по 2020 г., российская угольная отрасль демонстрировала высокие темпы развития. Наибольший спрос происходил в угледобывающем секторе (энергетический уголь и коксующийся уголь) – на 4% (по данным Минэнерго). По нашей оценке**, рынок горно-шахтного оборудования в стране ежегодно прирастал на 4,5–6%.
Расскажите о состоянии отечественного рынка горно-шахтного оборудования весной 2022 г.?
– Приведу цифры на примере угольной отрасли. Доля используемого отечественного горно-шахтного оборудования составляет в настоящее время при подземной добыче угля – 49,6%, при открытой добыче угля – 18,26%. Доля импортного оборудования среди отдельных видов основного оборудования для подземной добычи (механизированных крепей, добычных комбайнов) доходит до 80%, для гидравлических экскаваторов для открытой добычи угля составляет 100%, для карьерных самосвалов – более 80%, для оборудования по переработке и обогащению угля (гидроциклоны и флотационные машины) – более 64%.
Вместе с тем приведенные данные не полностью отражают современную ситуацию, требуется более глубокая оценка состояния рынка горно-шахтного оборудования и доли российских аналогов.
Что мешает росту производства отечественного горно-шахтного оборудования?
– Перед отечественным машиностроением стоит ряд вызовов.
Первый и, вероятно, главный – высокая закредитованность и высокая же стоимость кредитных ресурсов. Для промышленных предприятий характерна зависимость от доступности заемных средств, что связано с большими объемами закупок материалов, комплектующих и оборудования, длительными инвестиционными и производственными циклами. В отрасли накоплена большая кредитная нагрузка и наблюдается недостаток оборотных средств.
Второй вызов – системное недоинвестирование. Одной из главных проблем машиностроительного комплекса на сегодняшний день является тотальный износ основных фондов, который по экспертным оценкам превысил 50%. Коэффициент обновления на протяжении последних лет составляет 1–1,5%. Доля оборудования старше 20 лет превышает 40%.
Инвестиции в основной капитал машиностроительного комплекса составляют очень незначительную долю от их общего объема в экономику, при этом 75% капиталовложений формируется за счет собственных средств предприятий, 25% – это привлеченные средства, 5% – доля бюджетов всех уровней.
Третий проблемный момент – это, к сожалению, низкий уровень инноваций. При этом одним из важных показателей развития, вернее, одной из причин, объясняющих предыдущие неутешительные цифры, являются траты на НИОКР. Россия тратит немногим более 1% ВВП на НИОКР, при этом 70% финансирования обеспечивают государственные источники, и большая часть этих средств направляется в государственные НИИ. Крупные предприятия обеспечивают относительно небольшую часть исследований, а участие вузов в разработках и вовсе минимально.
Получается, что российские производители технических средств и программного обеспечения не могут удовлетворить потребности предприятий отрасли. В результате мы наблюдаем высокую зависимость от импорта на всем цикле работ – от геологического изучения недр до переработки полезных ископаемых.
Конечно, низкая операционная эффективность также мешает росту производства. По показателю производительности труда и оборачиваемости основных средств компании из России отстают от мировых аналогов уже много лет. Значение выработки на одного работника – это один из ключевых производственных показателей, используемых как для планирования производства, так и для оценки результатов труда и его эффективности. Рост производительности труда в России характеризуется серьезным замедлением.
В части эффективности операционной деятельности компании отечественного машиностроения значительно отстают от зарубежных аналогов. На меньшей площади конкуренты российского производителя могут собирать в 14 раз больше продукции.
Пятый вызов отрасли – это кадровый голод, вызванный дефицитом опытных специалистов, миграцией кадров в другие регионы, нехваткой квалифицированных молодых специалистов на производстве. В то же время существенной кадровой проблемой, снижающей эффективность производства, является профессионально-квалификационный дисбаланс (несоответствие компетенций квалификационным требованиям). Наблюдается недостаток компетенций, характерных для сервисной экономики и индустрии 4.0.
Назовите основные конкурентные преимущества локализации производства горно-шахтного оборудования в России, своего рода точки роста, и какие первоочередные шаги необходимо предпринять?
– Сейчас очевидно, что нужно развивать производство в России. Для этого необходимо предпринять следующие шаги: реструктуризировать кредитную нагрузку, повысить доступность заемного финансирования, создать единую информационную платформу сбора и удовлетворения потребностей в кадрах, оборудовании и финансировании, расширить внешнеэкономическое сотрудничество (Турция, Китай, Индия и пр.) в сфере технологий и инноваций. Кроме того, необходимо развивать механизмы трансфера технологий, стимулировать объединение в инновационные промышленные кластеры, предложить варианты льготного налогообложения.
И не менее важно вести активную работу с игроками горнодобывающей отрасли, развивая коммуникации внутри рынка, и реализовывать маркетинговые инициативы, стимулировать объединение в инновационные промышленные кластеры, регулировать деятельность поставщиков, организовывать круглые столы и штабы по обмену опытом, внедрять опыт честного бенчмаркинга на предприятиях.