Цифровизация обогатительной фабрики
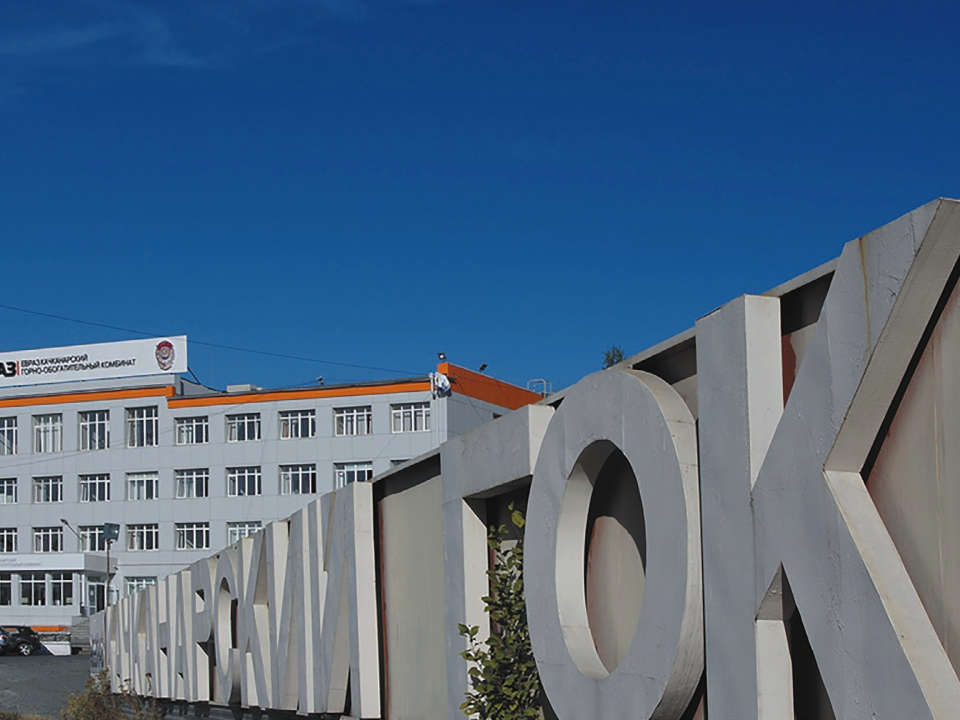
А.П. Блюденов Начальник обогатительной фабрики ЕВРАЗ КГОК
С.Ю. Макушев Главный обогатитель ЕВРАЗ КГОК
Д.В. Черепанов Главный специалист службы технико-технологического развития ЕВРАЗ КГОК
Д.А. Шнайдер Генеральный директор ООО «Белка Диджитал»
Продвинутая аналитика. Динамическое управление обогащением
В 2020–2021 гг. был внедрен первый цифровой проект «Продвинутая аналитика. Динамическое управление обогащением» (ПА ДУО). Основная задача – обеспечение целевого уровня Fe в концентрате при максимизации производительности технологических секций.
Функционал цифрового решения состоит из двух составляющих:
– Прогнозной модели качества производимого концентрата с учетом данных качества руды, поступающей на обогатительную фабрику;
– Оптимизационной модели для формирования рекомендаций операторам технологии обогащения по изменению производительности стержневых мельниц для дальнейшего управления качеством производимого концентрата.
Пример рекомендаций, выдаваемых ПА ДУО
Опыт эксплуатации ПА ДУО показал возможность применения цифровых решений для прогнозирования качества производимого концентрата и определения рекомендаций для повышения производительности стержневых мельниц. Среднее повышение производительности составило от 1 до 2 т/ч при снижении колебаний качества производимого концентрата.
При этом были определены направления дальнейшей проработки: система не учитывала работу дополнительных мельниц и насосов, подключение и выключение которых направлено на корректирование качества производимого концентрата.
Интеллектуальная система автоматического управления
технологическим процессом обогащения Во второй половине 2022 г. для дальнейшего развития ПА ДУО начата реализация проекта по разработке и внедрению интеллектуальной системы автоматического управления технологическим процессом обогащения (ИСАУТП ОФ). Данный проект реализуется совместно с компанией ООО «Белка Диджитал», г. Челябинск.
Основная задача – разработка системы автоматического управления технологическими параметрами обогащения: производительности стержневых мельниц, процента твердого в первой стадии измельчения, включения и отключения дополнительных мельниц измельчения и стадий сепарации для обеспечения производства концентрата стабильного качества. Также в фокусе внимания – увеличение извлечения ценного компонента в концентрат и снижение потерь с хвостами обогащения.
Перед началом внедрения системы в конце 2021 – начале 2022 г. компанией «Белка Диджитал» произведен аудит существующей технологии обогащения, включая кластерный анализ качественных показателей руды, поставляемой на фабрику.
Результаты кластерного анализа руды
Характеристика кластеров руды:
– 1-й кластер: высокое содержание Fe, низкая обогатимость, преобладают нормальнообогатимые руды. Самое низкое извлечение и высокое содержание Fe в ММС хвостах;
– 2-й кластер: «самый удобный», среднее содержание Fe, высокая обогатимость, преобладают легкообогатимые руды. Высокое извлечение, низкое содержание Fe в хвостах;
– 3-й кластер: «самый сложный», среднее содержание Fe, низкая обогатимость, содержат труднообогатимые руды. Качество поддерживается за счет допобогащения и перекачки между половинами;
– 4-й кластер: низкое содержание Fe, высокая обогатимость, высокая крупность, легкообогатимые руды с Северного карьера. Высокое извлечение, низкое содержание Fe в хвостах.
По каждому кластеру изучены исторические данные о количестве работающего оборудования, его производительности, качестве производимого концентрата и извлечении полезного компонента в концентрат. Проведена оценка эффективных и неэффективных режимов работы оборудования, в результате анализа определены возможности оптимизации процесса обогащения.
Перед началом реализации проекта было принято решение о внедрении дополнительного оборудования: плотномеров питания стадий ММС и автоматических задвижек пульпы для подключения дополнительных схем измельчения. Это позволит дополнительно повысить управляемость обогатительного процесса.
Интерфейс управления будущей системы ИСАУТП
В основу ИСАУТП BELKA заложены принципы модельно-упреждающего управления и адаптивности. В комплексе с решением задач управления изменениями на производстве это позволяет системе успешно функционировать в реальных производственных условиях с учетом следующих факторов:
– многосвязность технологического процесса, наличие большого числа альтернативных технологических схем;
– нестабильность технологического процесса из-за высокой изменчивости свойств входящей руды;
– влияние человеческого фактора, когда управление выполняют несколько специалистов с разными целями и задачами, опираясь на личные знания и субъективный опыт.
ИСАУТП BELKA в автоматизированном режиме управляет технологическим процессом:
– формирует рекомендации по динамическому изменению технологических параметров (загрузка мельниц по руде, подача воды, управление насосным оборудованием, мельницами доизмельчения и пульподелителями);
– формирует и передает в управляющие контроллеры значения управляемых параметров в автоматическом режиме под контролем оператора;
– контролирует соблюдение технологии и качество данных с приборов КИПиА.
Дополнительным инструментом повышения эффективности ИСАУТП выступает IIoT-система контроля технического состояния и шарового заполнения мельниц BELKA MILLVIBE. Опытно-промышленные испытания данной системы на одной из мельниц показали ее эффективность.
Рассматривается возможность тиражирования на другое оборудование обогатительной фабрики.
Разработка ИСАУТП выполняется поэтапно. Первый этап – проектирование системы, включая разработку математического, программного, технического и организационного обеспечения. Второй этап – строительно-монтажные и пусконаладочные работы и тестовая эксплуатация. Третий этап – запуск системы в промышленную эксплуатацию.
В настоящее время проект активно реализуется. Ожидаемый срок внедрения ИСАУТП от компании ООО «Белка Диджитал» – сентябрь 2023 г.
Уровнемеры параболических бункеров
В 2021–2022 гг. был внедрен программно-технический комплекс «Система контроля уровня (количества) руды в параболических бункерах», расположенных в корпусе обогащения перед сухой магнитной сепарацией. Основные задачи системы:
– определение и отображение уровня руды в питании каждой технологической секции в онлайн-режиме;
– отображение динамики изменения уровней относительно задаваемых предельных значений (критический верхний и критический нижний);
– визуальное информирование и предупреждение о необходимости загрузки бункера;
– обеспечение персонала ретроспективной технологической информацией (регистрация событий, регистрация параметров технологического процесса) для анализа, оптимизации и планирования работы оборудования и его ремонта.
Пример визуализации контроля уровня руды
Результат внедрения системы – снижение технологических простоев секций обогащения из-за неравномерного распределения руды по бункерам.
Автоматизация уровня зумпфов
В 2021–2023 гг. внедрена автоматизированная система управления регулировки уровня пульпы в зумпфах основной классификации технологических секций №1-29.
Это позволило решить несколько технологических задач:
– обеспечить поддержание стабильного уровня пульпы (исключить низкий уровень и переливы) в зумпфах перед насосами в питании основной классификации;
– минимизировать колебания давления пульпы на входе в гидроциклоны основной классификации;
– исключить «узкое место» в цикле основной классификации технологической цепочки обогащения.
Система реализована за счет применения:
– датчиков уровня пульпы в зумпфах;
– расходомеров узла регулирования подачи дополнительной технологической воды;
– датчиков давления узла регулирования подачи дополнительной технологической воды;
– датчиков давления на входе в коллектор батареи гидроциклонов;
– регуляторов подачи дополнительной технологической воды;
Схема системы автоматизации
Данные датчиков обрабатываются информационной системой и выводятся на рабочие места операторов пультов управления технологическим процессом.
По итогам испытания системы (апрель–май 2023 г.) отмечены следующие технологические эффекты:
– увеличение производительности технологических секций от 1 до 2 т/ч;
– повышение стабильности качества производимого концентрата.
Цифровой склад концентрата
В феврале 2022 г. завершено внедрение проекта «Цифровой склад концентрата». Это позволило выполнять ежесменное лазерное сканирование складов обогатительной фабрики с вычислением количества остатков готовой продукции для оперативного ведения технологического процесса производства концентрата.
Данная система работает за счет применения лазерной сканирующей установки Luftera LS-100-I, имеющей круговой обзор 360° и максимальную дальность сканирования 100 м.
Во время работы система закреплена на мостовом кране, который перемещается вдоль всего склада.
Сканер склада концентрата
Сканирование склада выполняется следующим образом:
– шаг 1. Лазерное сканирование склада во время движения крана;
– шаг 2. Формирование «Облака точек» при помощи ПО, идущего в комплекте системы;
– шаг 3. Измерение объема материала на складе и массы концентрата.
Получаемый результат:
– цифровая копия склада с высокой детализацией, получаемая за один проезд крана вдоль склада;
– измерение объемов штабелей с точностью маркшейдерского замера;
– возможность полной автоматизации измерения объемов.
Пример «Облака точек» склада
Онлайн-анализатор качества отгружаемого концентрата
В августе 2022 г. был внедрен проект «Поточные анализаторы химического состава концентрата» на конвейерах отгрузки концентрата из корпуса обогащения на фабрику окускования.
Онлайн-анализатор качества концентрата
Внедрение анализаторов позволило в онлайн-режиме получать данные по следующим показателям качества отгружаемого концентрата (Fe общее, CaO, V2O5, TiO2) и принимать решения по корректировке технологического процесса обогащения в случаях отклонения качества.
Интерфейс программы анализатора качества концентрата
Задачи дальнейшей цифровизации обогатительной фабрики
На период 2023–2025 гг. специалистами службы техникотехнологического развития (СТТР) рассматриваются к реализации следующие проекты по цифровизации обогатительной фабрики:
– Внедрение автоматизации работы катуче-реверсивных конвейеров на загрузке руды в параболические бункеры корпуса обогащения для равномерного распределения руды по технологическим секциям;
– Внедрение IIoT-датчиков для контроля загрузки мелющих тел и состояния основных подшипников мельниц. В 2022–2023 гг. проведены положительные опытно-промышленные испытания датчиков от компании ООО «Белка Диджитал» (г. Челябинск);
– Внедрение проекта «Цифровой склад концентрата 2.0» позволит дополнить существующие данные по объемам концентрата на складах данными по его качеству за счет информации с поточных анализаторов и данных цифрового подсказчика качества из проекта ИСАУТП.