Современные тенденции развития отечественного горного машиностроения
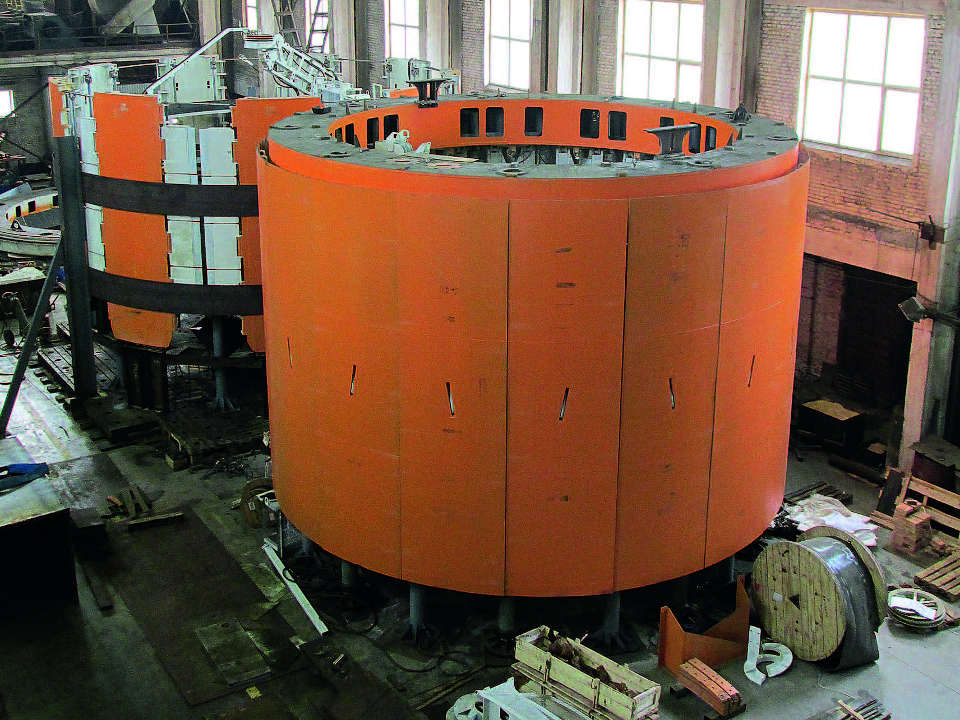
А.Н. Земсков, д-р техн. наук, советник председателя совета директоров, группа «КАНЕКС»
А.В. Иванов, директор по маркетингу, группа «КАНЕКС»
Прошло 13 лет с момента публикации статьи «Тенденции развития отечественного горного машиностроения» в журнале «Горная Промышленность» №1 (56) / 2005 [1]. Интересно проследить: а что же изменилось за эти годы?
Наверное, первый и достаточно неутешительный итог деятельности российских предприятий горного машиностроения за последние пятнадцать лет: ожидаемого технологического прорыва не случилось. Причин несколько. Это и мировой экономический кризис, и усложнение международной политической обстановки, и сохранившаяся у многих крупных промышленников привычка покупать заграничное. Впрочем, это объяснимо: несмотря на то что зарубежная техника для горной промышленности значительно дороже российской (по данным ученых НТЦНИИОГР (г. Челябинск), в общем случае в 5–26 раз), в среднем она обеспечивает производительность в 1,5–2 раза выше российских аналогов.
Выпуск современных высокопроизводительных горных машин определяет весь технический прогресс в горной промышленности страны. Повышение их качества, надежности и долговечности является залогом их конкурентоспособности на международном уровне.
Часто причиной невысокого качества и характеристик изделий является традиционная ориентация на черные металлы, когда использование неметаллических конструкционных материалов составляет всего 3–5% от общего объема.
И здесь мы в значительной степени отстаем от передовых стран, таких как, например, США, где доля неметаллических материалов в горном оборудовании составляет 15–20%. Между тем использование неметаллических материалов снижает вес оборудования, уменьшает энергозатраты на его производство и повышает срок службы на 25–30%.
В горном машиностроении СССР существовало распределение сфер производства той или иной горной техники. Украина всегда специализировалась на проектировании и производстве проходческо-добычных комбайнов (Ясиноватовский машзавод, Краматорский и Донецкий заводы горного машиностроения и т.д.). Азербайджан – на производстве оборудования для нефтяной отрасли. Белоруссия традиционно считалась сборочным цехом всего СССР: это и БЕЛАЗы, и МоАЗы, и трактора «Беларусь», и многое другое.
После распада СССР Россия была вынуждена компенсировать «пробоины» строительством новых заводов или реконструкцией старых производств. Начали набирать обороты Александровский машиностроительный завод и НПО «Искра» (Пермский край), машиностроительные предприятия Свердловской и Челябинской областей, заводы Кузбасса.
Но в середине второго десятилетия XXI в. в отрасли вновь начались серьезные проблемы. Фактически закрыты производства на ОАО «Кунгурский машиностроительный завод» (нефтегазовое машиностроение), ОАО «Александровский машзавод» (горнотранспортное машиностроение) (Пермский край). Крупнейший машиностроительный концерн России «Тракторные заводы», в который входят такие известные предприятия, как ОАО «Курганмашзавод», ОАО «Алтайский моторный завод» и другие, обременен долгами в 85 млрд руб. По мнению главы «Ростеха» Сергея Чемезова, концерн надо банкротить, ибо другого выхода нет.
А между тем речь идет о промышленной безопасности нашей страны! Сложность нынешней ситуации усугубляется тем, что разрабатываемые недра – наши, а технологии, сервис, специалисты – в основном иностранные. В частности, данные по Кузнецкому угольному бассейну свидетельствует, что до 85% горной техники – западного и китайского производства, 65–70% затрат на добычу и обогащение угля приходится на оборудование, запасные части и сервис зарубежных производителей или, другими словами, фактически из трех шахт или разрезов два работают на чужие страны.
И совсем не случайно, что в структуре экспорта России в 2017 г. доля машин, оборудования и транспортных средств составила всего 6,02% (в 2016 г. – 6,39%). В то же время эта позиция в структуре импорта заняла 45,62% (в 2016 г. – 44,26%). Основная доля поставок России в 2017 г. пришлась на минеральные продукты (60,37%), металлы и изделия из них (10,43%).
Справедливости ради стоит отметить, что все бывшие республики СССР в той или иной степени зависимы от импортной техники. Так, в Казахстане на долю машиностроительной продукции приходится 3,4% от общего объема экспорта и 40,6% – от импорта [2]. Доля казахстанского оборудования составляет около 13%, остальные 87% потребностей страны покрываются за счет зарубежных поставок [3]. И какие бы аргументы ни приводились по росту технологического потенциала, надо признать, что пока Россия – сырьевая страна. И не нужно, на наш взгляд, стыдиться этого: и Канада, и Чили, и ЮАР – страны с преобладанием сырьевого сектора над технологическим. По совокупному запасу полезных ископаемых на душу населения Россия превосходит США в 2–3 раза, Германию – в 5–6 раз, Японию – в 18–20 раз. Горно-нефтяной комплекс дает 78% ВВП России, а перевозка полезных ископаемых составляет 80% всех российских грузоперевозок!
Проблемой освоения месторождений полезных ископаемых в России является низкая плотность населения (9 чел/км2, в то время как в Европе – 165 чел/км2). Более того, свыше 70% объемов горно-металлургического комплекса приходится на северные районы России, где заселенность еще ниже [4].
Одновременно происходит и усложнение условий отработки месторождений полезных ископаемых. Наблюдается явная тенденция к росту глубины залегания продуктивных пластов и, следовательно, усложнению горнотехнических условий отработки. Это хорошо видно на примере разработки новых калийных месторождений (рис. 1). При добыче, транспортировке и переработке исходного сырья на обогатительных фабриках и металлургических заводах теряется до 40% полезных компонентов. Вот почему отношение к каждой технологической операции, в частности, к оснащению их высокопроизводительным оборудованием, должно быть очень серьезным.
На основании экспертного опроса специалистов калийной отрасли (38 человек) была составлена матрица состояния различных направлений функционирования калийных предприятий (рис. 2) [5]. Оценки выставлялись в процентах от 0 до 100. Максимальную оценку получила «перспектива спроса на конечную продукцию» – 90%, а самую низкую – «оборудование рудника» (50%). Естественно, эта экспертиза не является абсолютно надежной, но все-таки наталкивает на определенные выводы.
Отрадно отметить, что при усложняющихся правилах игры все явственнее составляют конкуренцию иностранным производителям отечественные машиностроители. К ним можно отнести Скуратовский опытно-экспериментальный завод (Тульская обл.) и группу «КАНЕКС». Так, например, важным моментом в создании современного горного оборудования является комплексность его поставки, которая предполагает увязку отдельных элементов (аппаратов) технологической цепочки: предоставление инжиниринговых услуг, доступность запасных частей, модернизацию оборудования, согласование разрешительных документов на его эксплуатацию.
Рис. 3 Общий вид комбайна типа СПКВ
Примером такого подхода в выпуске стволопроходческого оборудования является Скуратовский опытно-экспериментальный завод. Предприятие приступило к серийному изготовлению стволопроходческих комбайнов типа СПКВ (рис. 3) для строительства вертикальных шахтных стволов с монтажом комбинированной тюбинго-бетонной крепи и использованием механизированного разрушения и отгрузки породы. Конструкция новых комбайнов типа СПКВ воплощает в себе опыт эксплуатации двух ранее произведенных стволопроходческих агрегатов АСП-8.0 и АСП-7.0, успешно примененных в 2011–2015 гг. на строительстве стволов на калийном руднике ОАО «ЕвроХим» (Пермский край).
Следует отметить, что комбайн СПВК имеет ряд преимуществ в сравнении с аналогом иностранного производства. Во-первых, это взрывобезопасное исполнение, а не общепромышленное, которое «обеспечивает» целый ряд сложностей при пересечении газонасыщенных прослоев и пород.
Во-вторых, у комбайна СПКВ более простая и эффективная система удаления отбитой породы из забоя. В-третьих, цена в четыре (!) раза ниже.
Вывод: российские стволопроходческие комплексы являются одними из лучших в мире и способны обеспечить шахтопроходческие организации качественным современным оборудованием. Серьезные технические наработки в области рудничной электровозной откатки имеет ОКБ «Микрон» (входит в группу «КАНЕКС»). Конструкторами предприятия разработана оригинальная конструкция вагонеток (на базе выпускавшихся серийно вагонеток ВГ-4,5), позволяющая перевозить больший объем руды [6]. Так, за счет изменения геометрии чаши увеличен ее объем с 4,5 до 5,0 м3, а также обеспечена большая прочность самого кузова за счет усиления силовой рамы (утолщены ребра жесткости) и увеличения опорной базы. Кроме того, улучшена геометрия опоры колесной пары и модернизировано сцепное устройство. При этом вагонетки разгружаются теми же опрокидывателями. То есть модернизация оборудования не повлекла за собой модернизацию инфраструктуры. Новая модификация получила название ВГ-5М. Сегодня она широко используется на рудниках Заполярного филиала ПАО ГМК «Норильский никель».
Рис. 4 Электровоз шахтный К-17М
Модернизации подвергся и сам шахтный электровоз Кu14МА (рис. 4), что обеспечило ему ряд преимуществ над базовым вариантом (модификация получила индекс К-17М):
- увеличение тягового и тормозного усилия на 20%;
- замена электрооборудования постоянного тока на переменный с частотным регулированием (реализовано на стандартных электродвигателях и преобразователях частоты);
- модульная компоновка силового оборудования с возможностью оперативной замены отдельных силовых электрических модулей;
- наличие двух раздельных каналов питания силового оборудования (возможна работа на одном двигателе);
- предусмотрено резервное питание (10 с тяги без контакта с сетью) на суперконденсаторах;
- установлен бортовой компьютер с регистратором параметров работы электровоза; - дистанционное управление и электронная система безопасности.
Еще один пример работы «Микрона» в области повышения эффективности вагонеток – изменение конструкции зарубежных вагонеток с донной разгрузкой в рамках российской программы импортозамещения для АО «Кольская ГМК». При сохранении габаритных размеров вагонетки была усовершенствована конструкция колесной пары, усилены рама днища и передняя стенка кузова вагонетки.
Как видим, мы вполне способны поставлять на рынок конкурентоспособные продукты. Но в нынешних условиях, когда в Россию хлынул поток техники иностранного производства, отечественные машиностроители определенно нуждаются в протекционизме. В этой связи в прессе периодически поднимаются вопросы о необходимости введения или, наоборот, отмены специальных защитных мер защиты.
Очевидно, что полное эмбарго на импорт обернется колоссальными стратегическими потерями для России и большими издержками на сохранение неэффективных производств. В то же время нельзя не признать, что конкуренция полезна, однако в условиях существующих провалов внутреннего рынка она становится разрушительной для отечественных предприятий. Неразвитость инфраструктуры и высокие административные барьеры в действительности только усиливают позиции импортеров в ущерб внутреннему производителю.
На наш взгляд, оздоровление российского машиностроения должно носить комплексный характер, сочетающий элементы двух вышеотмеченных позиций.
Во-первых, действие защитных мер следует ограничивать по времени, например, до 3–5 лет (такова продолжительность среднего инвестиционного цикла, в который способны встать на ноги рыночно ориентированные предприятия).
Во-вторых, необходимо привлекать капитал зарубежных инвесторов или открывать совместные предприятия с крупными иностранными машиностроительными компаниями по выпуску новейшего горно-шахтного оборудования.
Для сведения: в Польше и Чехии, например, иностранные инвестиции составляют $ 1,5–2 тыс./год на жителя страны, а в России – всего $ 50–100, т.е. в 20–30 раз ниже. Здесь, на наш взгляд, более предпочтительный вариант сотрудничества состоит в разработке новой горной техники совместно со странами бывшего социалистического лагеря, прежде всего с Польшей, Чехией и Словакией. Машины этих производителей в среднем в 2 раза дешевле западных аналогов. А что касается качества – они ненамного уступают им в надежности.
В-третьих, дополнять существующую номенклатуру машиностроительных предприятий уникальными продуктами. К таким видам техники, на наш взгляд, можно отнести новые модификации грузовых подвесных канатных дорог (ГПКД). В последние годы вопросами проектирования и выпуска оборудования для ГПКД активно занимаются предприятия Западно-Уральского машиностроительного концерна (г. Пермь) и группы «КАНЕКС». Российскими организациями разработаны и внедрены футерованные колеса роликовых батарей, новые конструкции отклоняющихся башмаков, системы принудительного выравнивания скоростей вагонеток и выравнивания интервалов между вагонетками и т.д. [7].
В-четвертых, при разработке новых образцов горной техники концентрировать ресурсы только на прорывных направлениях, где издержки выхода на рынок меньше, чем в освоенных производствах, и там, где можно опередить конкурентов. России необходимо прорваться в эпоху «интеллектуальной экономики» и лишь тогда можно рассчитывать на серьезных инвесторов, приток капиталов и подъем отечественной наукоемкой промышленности.
В-пятых, продолжать совершенствовать механизмы государственной поддержки и стимулирования инновационной деятельности отечественных машиностроителей. В последние годы Минпромторгом многое сделано для развития этой стратегически важной для экономики нашей страны отрасли, но пока, к сожалению, можно констатировать, что остановить падение внутреннего спроса на продукцию российских производителей не удалось.